DaoAI Story
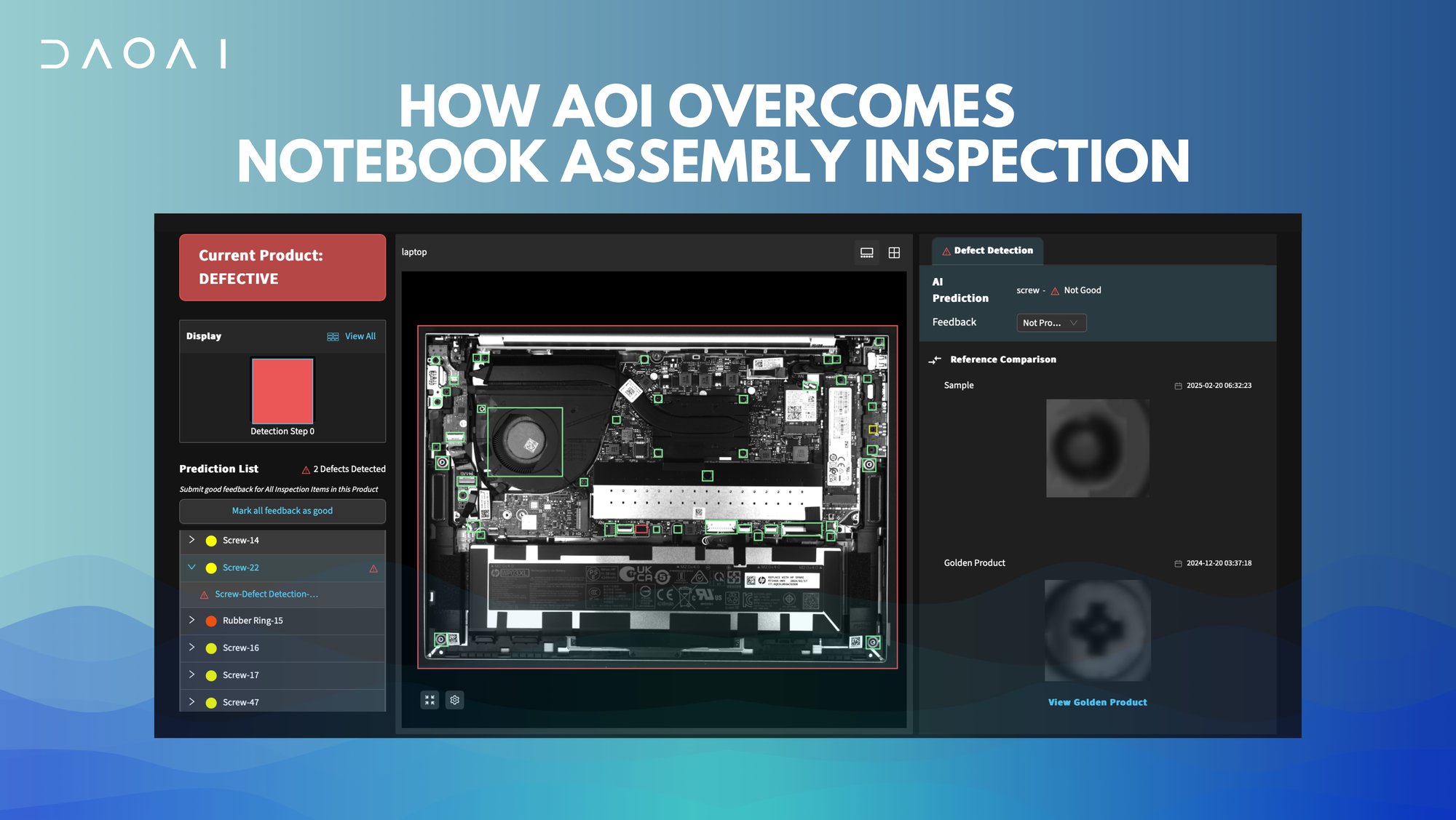
Currently, notebook assembly inspection faces numerous challenges and pain points:
- Diversity and Complexity of Components: The internal structure of a notebook is highly complex, consisting of numerous components such as the motherboard, CPU, hard drive, screen, and keyboard. Each with specific assembly requirements and inspection standards. For example, the positioning and connection methods of various interfaces on the motherboard, the screen-to-body adhesion, and the layout and responsiveness of keyboard keys all require meticulous inspection. Additionally, different notebook models may have significant design variations, further increasing the complexity of inspection. A particularly critical issue is the adhesion between the screen and the backlight panel, which must be rigorously controlled. Otherwise, defects such as light leakage, liquid leakage, or even backlight panel burnout may occur, severely affecting product quality and user experience.
- High-Speed Production and Real-Time Inspection Requirements: Modern notebook production lines prioritize efficiency, with increasing production speeds. Traditional inspection methods struggle to keep pace with the production line, making real-time, high-efficiency inspection difficult. Any delays in the inspection process can lead to defective products progressing to the next stage or even leaving the factory. Additionally, frequent adjustments to equipment and the production line necessitate an adaptable inspection system capable of rapid model switching to meet high-speed production demands.
- Dynamic Production Environment: The conditions on a notebook production line are constantly changing, with models being modified and quickly replaced. Factors such as temperature deformation and unstable lighting can affect the accuracy of inspection results. Maintaining the stability and reliability of the inspection system in such a dynamic production environment is a key challenge for notebook assembly inspection.
- Hidden Defects Are Hard to Detect but Have Serious Consequences: During notebook production, defective samples appear infrequently and are costly to obtain. The accuracy and efficiency of manual inspection make it difficult to detect defects when they do occur. This presents a significant challenge for training detection models based on sample learning. Maximizing the use of limited sample resources to enhance model generalization and detection accuracy is an urgent issue. More critically, some hidden manufacturing defects only become apparent during repairs, meaning enterprises may face explicit costs from mass recalls and implicit costs from brand reputation damage.
How AOI System Solves These Problems
Component Diversity and Complexity- Multi-Component Detection: The AOI system can inspect multiple components simultaneously. Using annotation tools, different components can be marked to ensure accurate recognition of each part.
-
Real-Time Inspection: The AOI system conducts real-time inspections on the production line. Its high-speed and precise detection ensures that every product and defect is identified promptly, preventing defective products from proceeding to the next stage.
-
Rapid Model Switching: The AOI system quickly adapts to the design variations of different laptop models by adjusting model parameters and annotations, enabling rapid mold switching to meet diverse production line demands.
- Defect Recognition: Leverages unsupervised anomaly detection algorithms to identify unknown defects, ensuring accurate inspection of every product.
- Optimization: The system enhances model accuracy through its feedback loop mechanism, making optimal use of limited sample resources and reducing dependency on defect samples.
On the product management page, click “New Inspection Works”.
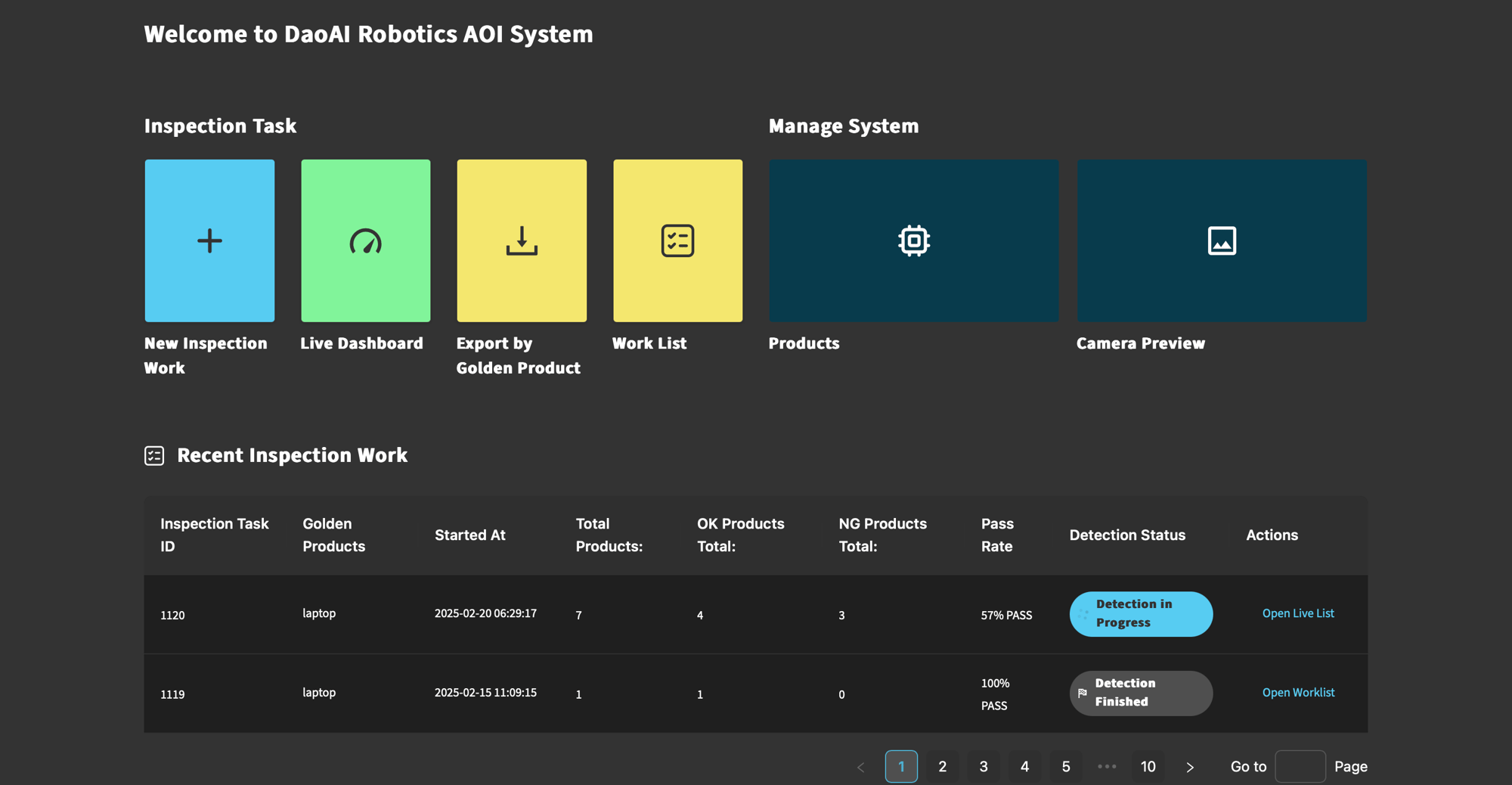
Use a high-precision camera to capture images of the laptop motherboard, ensuring that clear and complete images are collected. In the toolbar at the bottom right, click the labeling tool to accurately annotate each component in the image. For example, label the entire laptop as "product," and then label key components such as the motherboard, CPU, memory, hard drive, screws, and keyboard with corresponding tags. This process requires careful attention to detail to ensure that the model can correctly identify and detect each component.
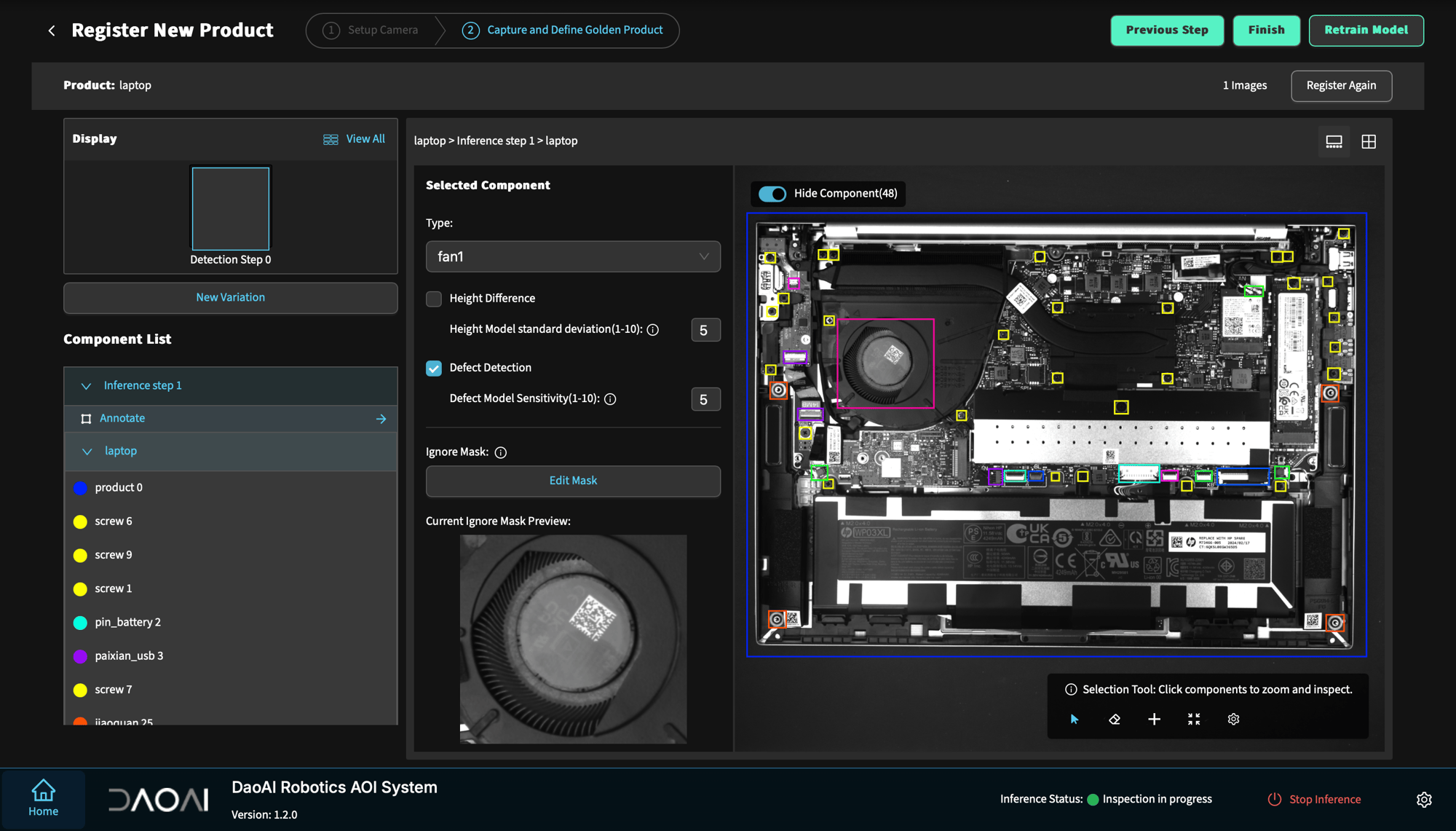
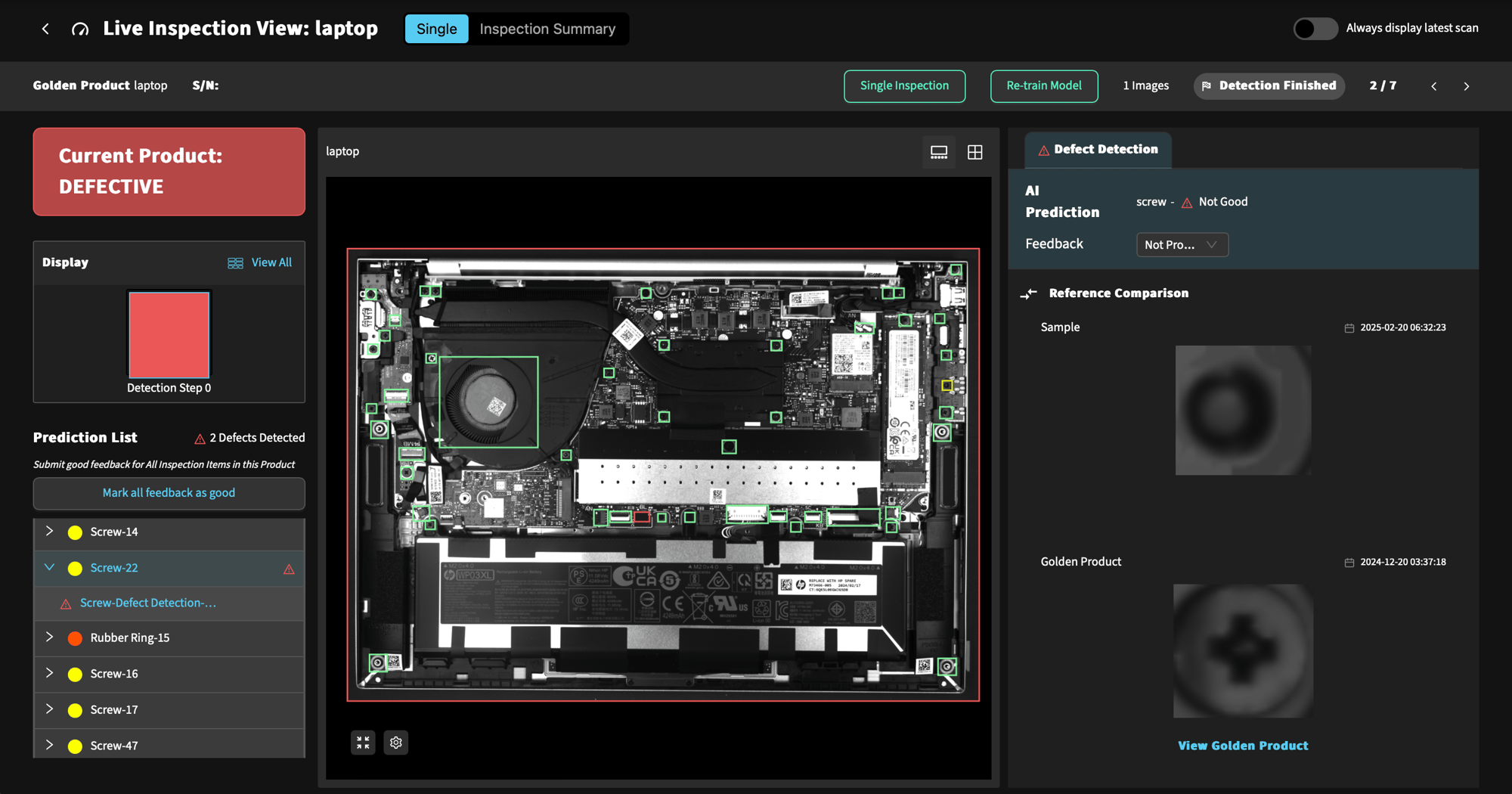
Illustration: Detection of an Incorrect Screw Installed
The DaoAI AOI system features a unique feedback loop mechanism that allows real-time optimization based on detection results. In rare cases of overkill or missed detection, users can manually mark the selected area/component as correct.
As shown in the illustration, if overkill occurs, simply mark the designated area as Good (a one-click option is available on the left to mark all selected areas as Good). Conversely, if a missed detection occurs, mark the corresponding laptop component as NG, then use the tool to highlight the erroneous area (such as component damage or assembly errors). Once completed, click to retrain the model. We recommend repeating this review process multiple times in special cases to maximize performance improvements.
Just as humans learn from mistakes, the DaoAI AOI system seamlessly integrates human feedback and rapidly retrains the model, enabling real-time continuous updates. This mechanism ensures that system accuracy improves over time.
The DaoAI AOI system brings a groundbreaking upgrade to laptop assembly inspection through fully positive sample learning, pixel-level detection, and a unique feedback loop mechanism:
-
Zero-Defect Sample Dependency: Requires only 1-20 high-quality non-defective samples to build the AI model, effectively addressing the high cost of defect data reproduction and the complexity of data collection and annotation.
-
Ultra-Fast & Accurate Detection: Achieves a detection speed of just 10 milliseconds per inspection area, with an initial accuracy rate of 99.7%—far surpassing traditional AOI systems—while continuously improving through feedback loop learning to meet the high-quality, high-efficiency demands of laptop production lines.
-
Unknown Defect Detection: Utilizes unsupervised anomaly detection algorithms to excel in identifying potential defects such as wear, scratches, and foreign contamination, enabling timely detection and warnings to prevent batch-quality issues.
-
Fast Review & Record Keeping: A highly integrated platform supports rapid model iteration and feedback while maximizing user convenience; it allows one-click access to past inspection records and abnormal areas/components for seamless data tracking and traceability.
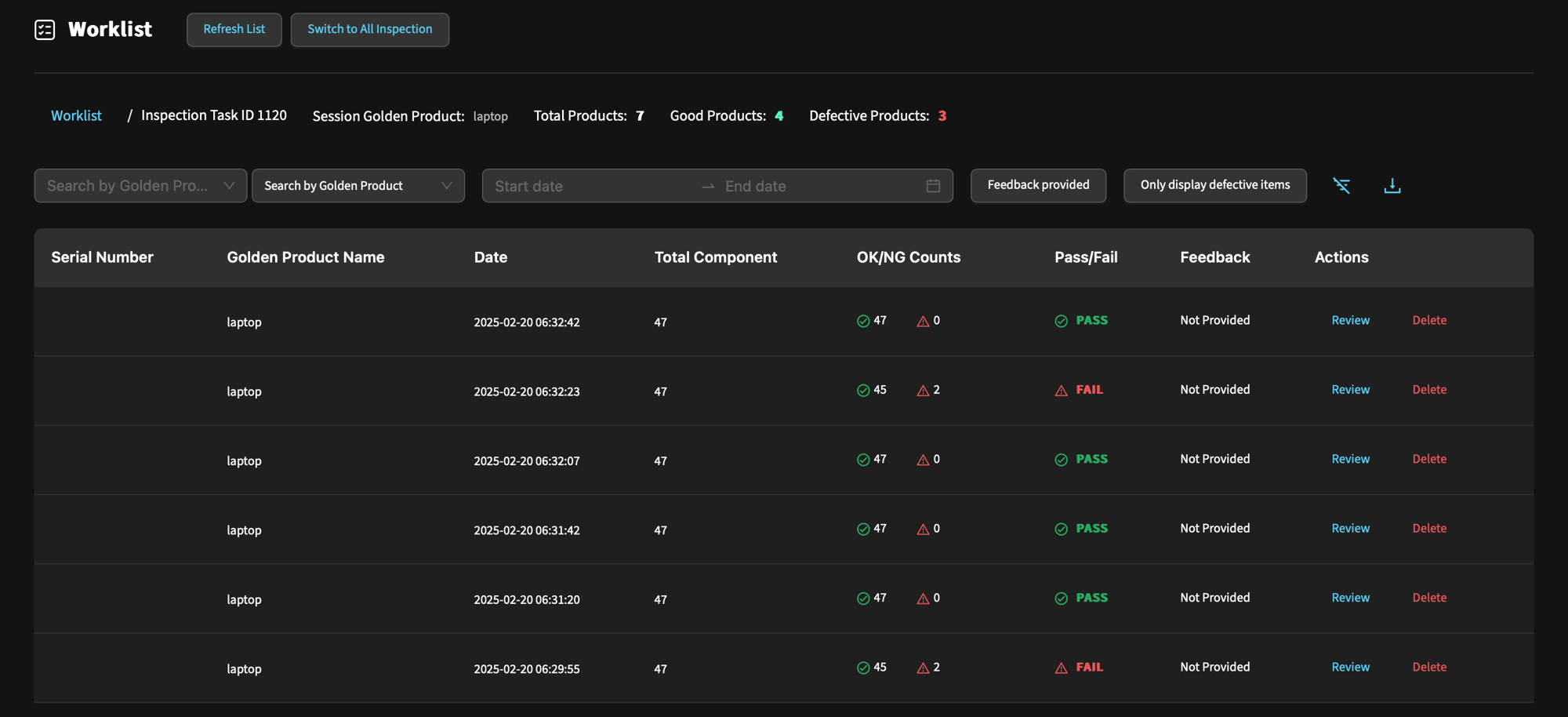
Please feel free to call and communicate with our technical team to experience the actual testing performance of AOI.
We will provide you with intelligent inspection reports, and DaoAI will revolutionize notebook assembly inspection for you.