Computers have undoubtedly become an essential tool in modern life, and the keyboard, as the accessory that users have most direct interaction with, its quality directly impacts the user experience. As a core component of the keyboard, keycaps face numerous challenges in their inspection: The variety of keyboard styles and the different words and symbols on the keycaps. Which means the training process requires a large number of samples.
Moreover, issues such as tiny defect sizes and environmental interference make the detection process both complex and time-consuming. DaoAI provides a solution for keyboard manufacturers by identify unknown defects through using only positive samples. Combined with high-precision imaging and image preprocessing, this approach reduces sample collection costs while effectively overcoming challenges like subtle and inconspicuous defects, significantly improving overall detection efficiency.
Detection Challenges
The keyboard market today is highly diverse, ranging from standard keyboards to mechanical keyboards, membrane keyboards, and ergonomic keyboards. Each type of keyboard has different specifications and molds, with variations in the number, layout, shape, and size of keycaps. This makes it extremely difficult to segment and identify individual keycaps. Traditional detection methods struggle to meet such complex and diverse inspection requirements, especially when rapid detection is needed on large-scale production lines.
During the manufacturing process, keycaps may develop various tiny defects, such as barely visible scratches, dents, and bubbles. Under an 8K-resolution line-scan camera, the smallest defect may measure as little as 9 pixels on one side. These minuscule defects may not be prominent in images, making them easy to overlook or misjudge. This imposes extremely high demands on the precision and sensitivity of the detection system. Traditional inspection methods often fail to accurately identify these tiny defects, leading to detection inaccuracies.
Despite various measures taken to minimize dust and other contaminants in keyboard production lines, it is impossible to completely eliminate dust. Dust particles may settle on the surface of keycaps, creating white speck-like interference that can be mistaken for actual defects during detection. This increases the complexity and difficulty of the inspection process. Accurately identifying keycap defects while accounting for dust interference remains one of the key challenges in keyboard quality inspection.
DaoAI Solution
In real-world applications, DaoAI AOI system learns only from single positive samples to understand the standard characteristics of a product. During inspections, any detected anomalies are marked as potential defects for operators to review and confirm. If verified as actual defects, the system allows training personnel to highlight the defective area, ensuring future inspections prioritize these features. Similarly, if a false positive occurs, the platform provides a one-click feedback option to classify the anomaly as a normal sample, preventing unnecessary false alarms and optimizing model performance.
Paired with DaoAI’s specialized high-resolution cameras, the system captures the finest details of keycaps, ensuring that even the smallest defects are accurately detected. Also enhancing detection accuracy and reliability by highlighting keycap’s structural and defect features, segmenting key areas, reducing background interference, and improving image contrast.
The DaoAI AOI system is designed to handle the complexity of detecting large volumes of keycaps across various keyboard types. It can automatically classify and inspect different keyboard models, significantly boosting detection efficiency. To further optimize performance, the system builds a diverse keyboard model database, covering various keyboard types, keycap shapes, and sizes to meet different inspection needs.
The DaoAI AOI system delivers ultra-fast, precise detection, completing inspections within milliseconds per keycap with an initial model accuracy exceeding 99%. Its unique feedback learning mechanism allows AI to learn from mistakes, updating anomaly data in real time and rapidly iterating the model to keep pace with high-speed production lines.
On actual production lines, DaoAI AOI integrates with automated control systems (e.g., Siemens EasyCube) to synchronize assembly and inspection processes. During fast-paced production, the system enables seamless defect detection, rechecking, and correction, ensuring that every keycap is inspected before advancing to the next stage. As an all-in-one platform, it centralizes data management and provides visualized quality monitoring charts, allowing manufacturers to trace defects, adjust production parameters, and maintain stable operations on the production line.
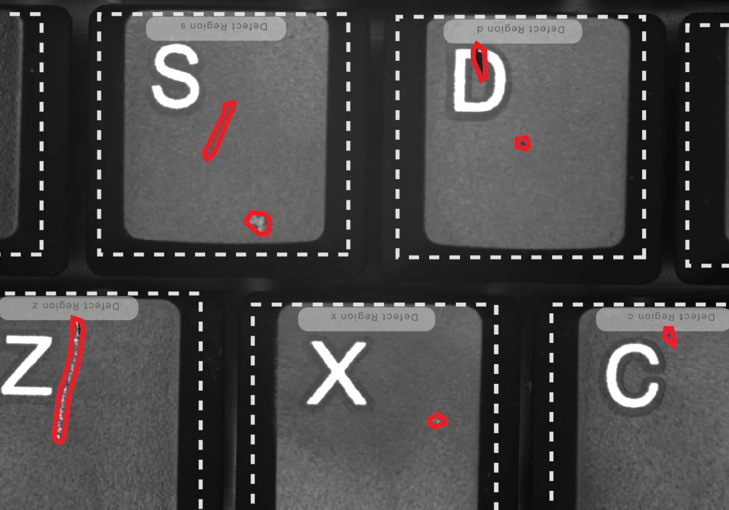
The DaoAI AOI system offers an efficient solution for keyboard inspection through its self-developed AI model, combined with high-precision imaging and a feedback mechanism. It effectively addresses challenges such as the wide variety of keyboards, tiny defects, and complex production environments, ensuring accuracy, performance, and reliability in defect detection.
By implementing the DaoAI AOI system, keyboard manufacturers can enhance production efficiency, improve product quality, and reduce manufacturing costs—ultimately delivering higher-quality, more reliable keyboards to users.
Contact us now to create a tailored AI visual inspection solution for you!
FAQ
1. What challenges are involved in inspecting keyboard keycaps during manufacturing?
Inspecting keyboard keycaps presents several challenges:
-
Variety of Keyboard Designs: Keyboards come in various types—mechanical, membrane, ergonomic—with differing keycap shapes, sizes, and layouts, complicating standardization in inspection processes.
-
Tiny and Subtle Defects: Defects such as minute scratches, dents, or bubbles can be as small as 9 pixels in high-resolution images, making them difficult to detect with traditional methods.
-
Environmental Interference: Dust particles and other contaminants can settle on keycaps, potentially being misidentified as defects, thereby increasing false positives.
2. How does DaoAI's AOI system address these inspection challenges?
DaoAI's Automated Optical Inspection (AOI) system tackles these issues through:
-
Positive Sample Training: The system learns from defect-free samples, identifying anomalies without requiring extensive defect datasets.
-
High-Resolution Imaging: Utilizing specialized cameras, the system captures detailed images, enabling the detection of minute defects.
-
Advanced Image Processing: Techniques like background suppression and contrast enhancement help distinguish actual defects from environmental noise.Good Keyboard
3. Can the system adapt to different keyboard models and layouts?
Yes. The DaoAI AOI system is designed to handle a wide range of keyboard types. It can automatically classify and inspect various keyboard models by building a diverse database covering different keycap shapes and sizes, thereby enhancing detection efficiency across multiple product lines.DaoAI
4. How does the system improve over time with operator feedback?
The system incorporates a feedback mechanism where operators can:
-
Confirm Defects: When an anomaly is detected, operators can validate it as a defect, prompting the system to prioritize similar features in future inspections.
-
Correct False Positives: If a non-defective area is misidentified, operators can reclassify it, allowing the system to adjust and reduce unnecessary false alarms.
This continuous learning loop ensures the system becomes more accurate and reliable over time.
5. What benefits does implementing DaoAI's AOI system offer to manufacturers?
By adopting DaoAI's AOI system, manufacturers can achieve:
-
Enhanced Quality Control: Accurate detection of defects ensures higher product quality.
-
Increased Efficiency: Automated inspections reduce the time and labor required for quality checks.
-
Cost Savings: Early detection of defects minimizes waste and reduces the need for rework.
-
Scalability: The system's adaptability allows for seamless integration across various production lines and keyboard models